In the rapidly evolving construction industry, precision, efficiency, and quality assurance are paramount. MEP (Mechanical, Electrical, and Plumbing) surveys, troubleshooting, and thermographic surveys are vital tools in ensuring a project's success. Errors or inefficiencies within these systems can lead to significant cost overruns, delays, and potential safety issues. MEP surveys, troubleshooting, and thermographic tests are preventive measures that identify problems early on, optimise system integration, and enhance operational efficiency.
This guide will cover the importance of MEP surveys, thermographic surveys, benefits, best practices, common challenges, current trends, and the outlook for these services in the construction industry.
What Are MEP Surveys and Troubleshooting?
MEP surveys evaluate the condition and functionality of mechanical, electrical, and plumbing systems in a building. These surveys focus on ensuring that each system operates correctly, identifying potential issues, and verifying compliance with current standards and codes. MEP surveys are essential in both new constructions and existing buildings, providing a detailed overview of system conditions and potential upgrades.
MEP troubleshooting, on the other hand, is a more specific intervention process. It involves identifying and resolving issues within the MEP systems, such as electrical faults, HVAC inefficiencies, or plumbing malfunctions. By diagnosing these issues early, MEP troubleshooting reduces the risk of costly repairs and ensures a building’s operational safety and efficiency.
What Is a Thermographic Survey?
A thermographic survey employs infrared cameras to detect variations in temperature across building surfaces, which can indicate issues such as insulation problems, moisture ingress, or electrical faults. This non-invasive survey method is invaluable for pinpointing problems in areas that are difficult to access or potentially hazardous. In construction, thermographic tests are typically performed during initial installation phases or as part of regular maintenance to ensure systems remain functional and safe.
What are the Benefits of MEP and Thermographic Surveys?
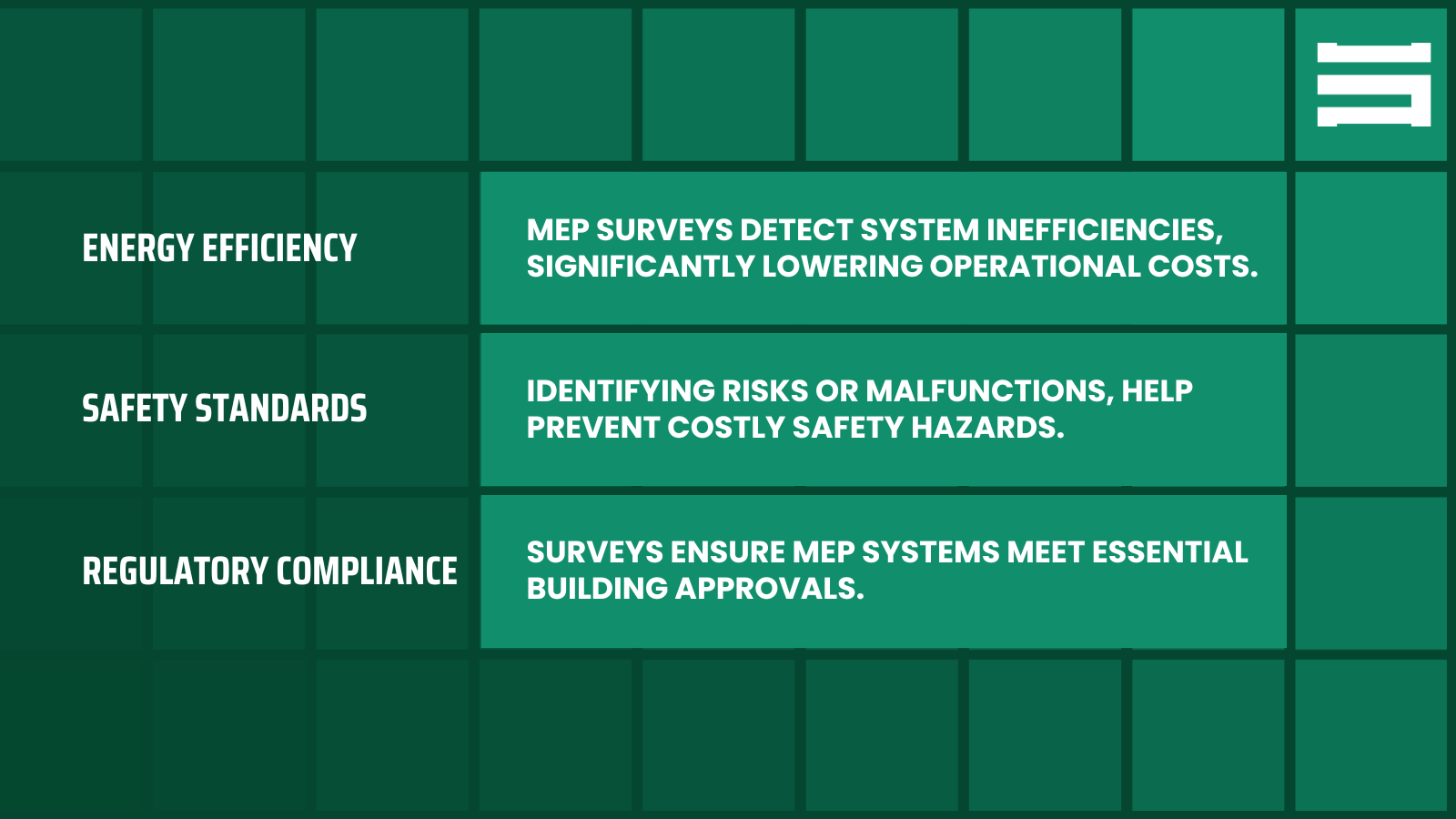
- Increased Efficiency: By detecting inefficiencies within MEP systems, surveys help improve energy consumption, ultimately lowering operational costs.
- Enhanced Safety: Identifying potential risks, such as electrical overheating or HVAC malfunctions, reduces safety hazards.
- Improved Compliance: Surveys help ensure that all systems meet regulatory standards, which is particularly important for certifications and building approvals.
- Cost Savings: Early detection of issues mitigates the need for expensive repairs or replacements down the line.
- Accurate Decision-Making: Detailed data from these surveys provides essential insights for maintenance, renovations, or retrofitting plans.
The Best Practices in MEP and Thermographic Surveys
Achieving optimal results in MEP (Mechanical, Electrical, and Plumbing) surveys and thermographic testing requires a strategic approach that combines technology, skilled professionals, and detailed documentation. Here are some best practices to guide successful MEP survey and troubleshooting processes, ensuring efficiency, safety, and long-term project value.
1. Integrate BIM for MEP Clash Detection Services
Building Information Modelling (BIM) technology has revolutionised MEP design and surveying by providing a 3D digital representation of building components. In MEP surveys, BIM enables clash detection, allowing surveyors to identify and visualise potential conflicts between mechanical, electrical, and plumbing elements within the building structure before actual construction. By pinpointing conflicts early, BIM minimises costly delays and reduces the likelihood of rework, both of which contribute to significant savings in time and budget.
Moreover, MEP clash detection services using BIM allow for better coordination among project stakeholders. With a comprehensive model accessible to all parties, everyone involved can see the same issues, make informed adjustments, and contribute to a more integrated design process. As construction projects become increasingly complex, the role of BIM in enhancing MEP survey accuracy and collaboration is indispensable.
2. Use Qualified MEP Consultants
The expertise of an experienced MEP consultant is invaluable for ensuring that surveys and inspections meet the latest industry standards and are executed with precision. Qualified MEP consultants bring a wealth of knowledge regarding regulations, best practices, and potential pitfalls. They can anticipate challenges that may not be immediately apparent, advising on both immediate troubleshooting and long-term system maintenance.
Additionally, having skilled consultants ensures that every element of the MEP survey, from thermographic analysis to testing electrical systems, is conducted with a focus on quality and compliance. This not only safeguards the building's safety and efficiency but also helps in meeting regulatory standards, which can be especially critical in complex or large-scale projects.
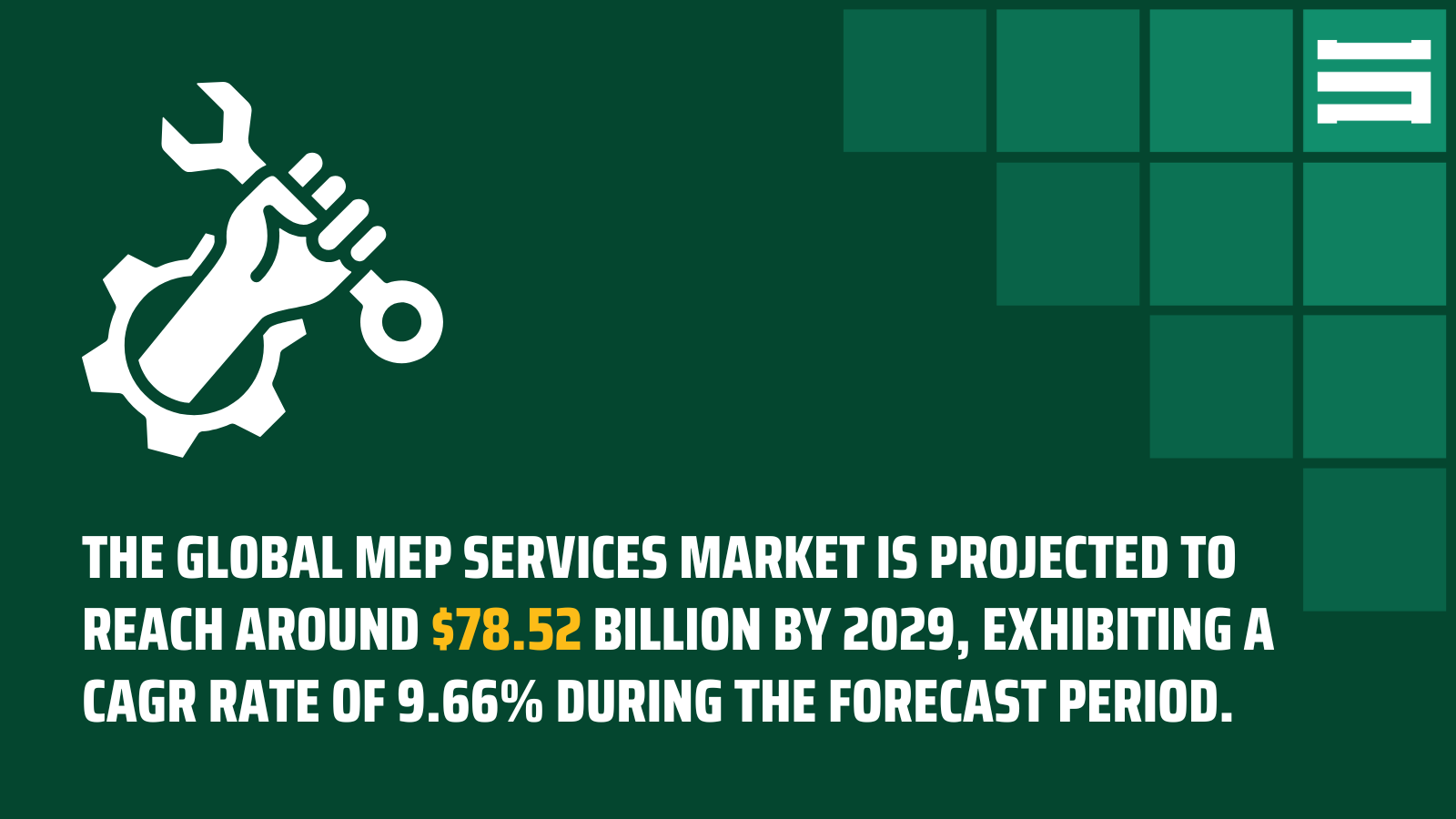
3. Perform Regular Maintenance Inspections
Routine thermographic inspections and regular MEP surveys are crucial for early detection of issues that could compromise the safety and functionality of building systems. For example, thermographic tests, which use infrared technology to measure temperature variations, can reveal hotspots or temperature anomalies in electrical panels, HVAC units, and insulation. Such anomalies often indicate potential failures or inefficiencies, allowing facility managers to address problems before they escalate.
Regular inspections are not only beneficial for new construction projects but also for existing buildings. Over time, MEP systems degrade or experience wear and tear, and routine checks are essential to monitor system health and performance. In the long run, these inspections minimise the risk of major malfunctions, contribute to energy efficiency, and extend the lifespan of essential infrastructure.
4. Document Findings Thoroughly
Thorough documentation is a foundational element of successful MEP and thermographic surveys. Detailed records of all surveys, tests, and troubleshooting efforts provide an essential reference for future maintenance, compliance audits, and project handovers. Comprehensive handover documentation helps maintain continuity, especially when staff changes occur, and supports transparency among stakeholders by recording each decision and action taken.
Documentation should include the initial conditions observed, specific anomalies found, methods used in troubleshooting, and corrective measures implemented. For example, thermographic survey records should detail temperature readings, identified hotspots, and corrective recommendations. Proper documentation is particularly important in the construction industry, where records are often required for compliance purposes and can serve as evidence in case of disputes or inspections.
5. Ensure Structural Drawing Integration
Integrating MEP surveys with the building's structural drawings is essential for compatibility and cohesion in design. Structural drawings serve as the blueprint for a building’s layout, detailing where walls, supports, and foundations will be. Aligning MEP plans with these structural specifications ensures that each mechanical, electrical, and plumbing element is properly positioned within the building’s overall design.
For instance, HVAC ducting, electrical conduits, and plumbing lines need to work around the structural components of a building. Ensuring alignment between MEP layouts and structural drawings reduces the risk of clashes and maximises the efficiency of the layout. Structural drawing integration ultimately enhances the quality and feasibility of MEP system installations, avoiding on-site conflicts that can cause project delays.
Challenges and Opportunities in MEP Inspection and Testing
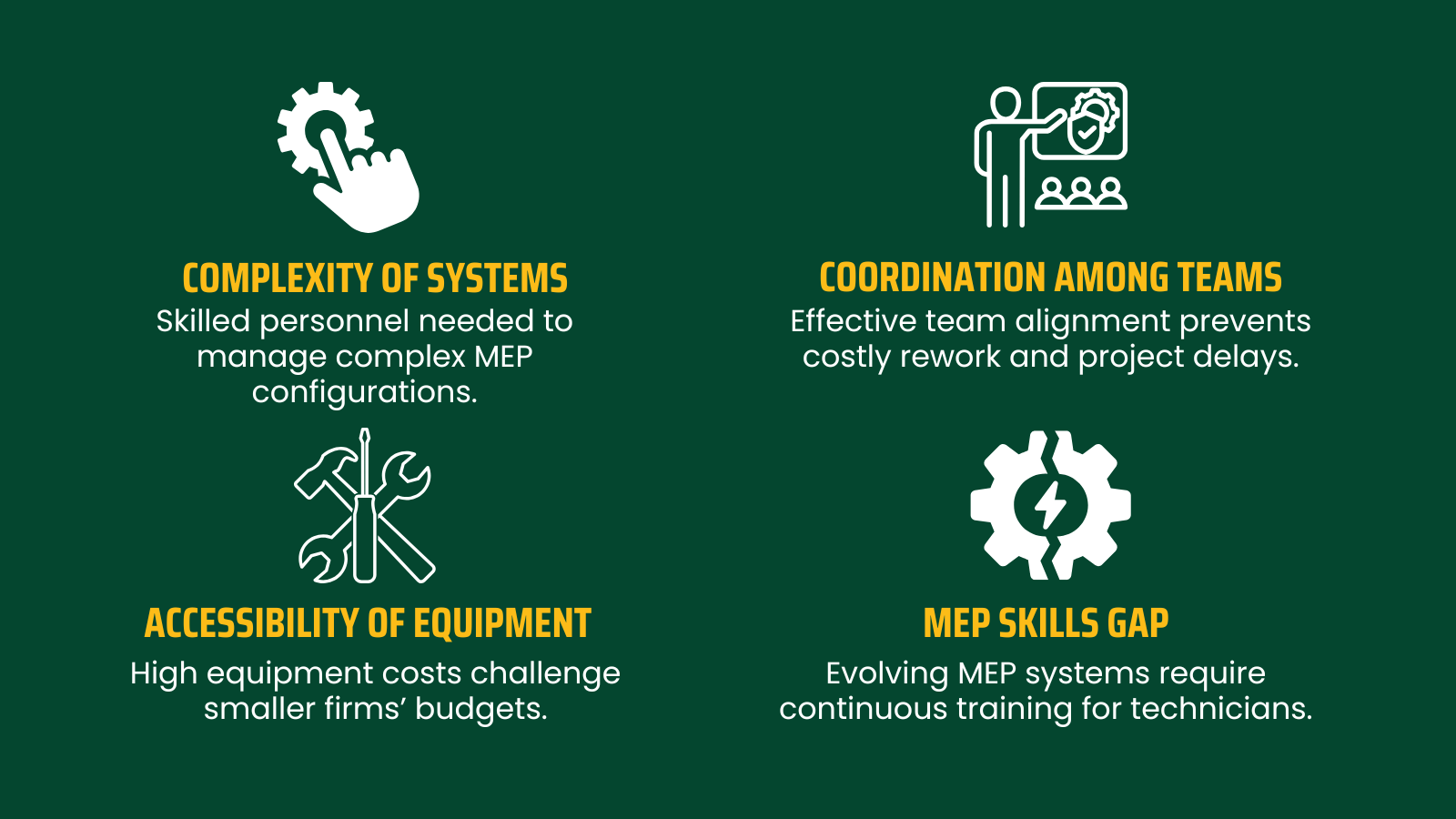
Challenges in MEP Inspection and Testing
- Complexity of Systems: Modern buildings incorporate highly intricate MEP configurations that serve diverse purposes, from energy efficiency to advanced climate control. This complexity demands skilled and experienced personnel to conduct effective inspections and troubleshooting. As systems grow more advanced, technicians must not only understand each component individually but also assess how they interact as part of a cohesive system. For some firms, this necessitates hiring specialised experts, increasing the overall costs of projects.
- Coordination Among Teams: Aligning the work of mechanical, electrical, and plumbing teams is critical but can be challenging, especially in large construction projects. Each system has its requirements and installation timelines, and these must be seamlessly integrated within the project. Inadequate coordination can lead to clashes or design inconsistencies that require costly rework. Effective coordination often requires implementing tools like Building Information Modelling (BIM) and holding regular team meetings to keep all parties aligned on updates and adjustments.
- Cost and Accessibility of Equipment: The tools and technologies used for MEP and thermographic inspections—such as infrared cameras and specialised diagnostic devices—are essential for accuracy and precision. However, these tools come with substantial costs, making initial investment a potential barrier for some firms. Additionally, ongoing equipment maintenance and upgrades can contribute to higher operational costs over time.
- Skills Gap: With the fast-paced evolution of MEP systems, maintaining a workforce with the necessary skills for inspection and testing is challenging. The expertise required to operate advanced equipment and conduct detailed analyses means that ongoing training and development are essential for technicians. As systems grow more complex, the demand for highly skilled personnel increases, and the available pool of qualified technicians may not be sufficient to meet this demand, posing a skills gap for many firms.
Opportunities Available in MEP Inspection and Testing
- Advanced Tools like BIM for Enhanced Coordination: BIM technology presents an exciting opportunity to address coordination challenges by offering a collaborative platform for integrating MEP systems with the broader building design. With BIM, different teams can identify potential clashes early in the design phase, significantly reducing the risk of on-site conflicts and rework. By adopting BIM, firms can streamline coordination and provide a more efficient and unified approach to MEP installations.
- Cross-Disciplinary Collaboration: The need for cohesive integration of MEP systems within construction projects encourages collaboration among traditionally separate disciplines. Through regular meetings, shared goals, and collaborative problem-solving, MEP teams, architects, and structural engineers can work more closely to achieve optimal results. This cross-disciplinary approach fosters innovation and allows firms to leverage diverse expertise, setting them apart as industry leaders in holistic project management.
- Investment in High-Precision Equipment as a Competitive Advantage: While the cost of advanced diagnostic equipment is a challenge, it also offers an opportunity for firms willing to invest in high-quality tools. Enhanced tools like thermographic cameras provide more accurate, reliable data, enabling faster and more precise troubleshooting and maintenance. Firms that prioritise quality equipment position themselves as high-standard service providers, potentially attracting clients who value long-term reliability and precision.
- Upskilling and Professional Development: Addressing the skills gap offers firms the opportunity to become industry leaders by investing in continuous training for their teams. Companies that provide upskilling programs and foster ongoing professional development not only meet current demands but also prepare their workforce for future advancements in MEP technology. As a result, firms that prioritise education and development can differentiate themselves by offering services with a high level of expertise and adaptability.
Current Trends in MEP and Thermographic Testing
The MEP and thermographic survey industry is influenced by several key trends:
- Growth of BIM in MEP Clash Detection Services: BIM technology continues to gain traction in construction. It enables comprehensive 3D modelling and clash detection, significantly improving design accuracy and reducing on-site conflicts.
- Increased Demand for Infrared Thermographic Survey: Infrared technology is becoming more prevalent due to its non-invasive nature and its ability to provide insights into hidden structural and operational issues.
- Sustainable and Energy-Efficient Solutions: With a greater focus on sustainability, thermographic surveys are essential in identifying energy leaks and insulation deficiencies, contributing to greener building initiatives.
- Focus on Digital Documentation: Cloud-based data storage and digital project management tools allow for easy documentation and sharing of survey findings, enhancing collaboration and accessibility.
Outlook on MEP and Thermographic Survey Services in Construction
The global MEP services market was valued at approximately USD 44.75 billion in 2023 and is projected to reach around USD 78.52 billion by 2029, exhibiting a Compound Annual Growth Rate (CAGR) of 9.66% during the forecast period.
The future of MEP surveys, troubleshooting, and thermographic inspections in the construction sector looks promising. The integration of BIM and thermographic technology is expected to enhance accuracy, reduce costs, and improve project timelines. As regulatory requirements evolve, MEP systems must meet stricter compliance standards, making regular inspections more critical than ever.
Conclusion
In the dynamic and complex world of construction, the importance of MEP and thermographic surveys cannot be overstated. These surveys not only protect your investment but also improve efficiency, safety, and sustainability. Partnering with an experienced provider, such as Stonehaven, can make all the difference in delivering successful, cost-effective construction projects that stand the test of time.
About us
Stonehaven is a trusted project management company and construction consultant based in Dubai, offering comprehensive construction management services across the UAE with offices located in Dubai, UK and Sri Lanka. As one of the leading project management companies in Dubai, we manage projects from inception to completion, ensuring quality, efficiency, and cost-effectiveness at every stage.
We deliver value through expert project management consultancy services, tailored to meet the unique needs of each client. Our core services include Cost Management, Project Management, Construction Supervision, Engineering Support, Design Support, and Marketing & Communications. Whether you’re looking for construction consultants or project managers in the UAE and wider GCC region, Stonehaven is your trusted partner for achieving excellence in your next project.
Stonehaven is a leading provider of MEP and thermographic survey services. With a commitment to accuracy, innovation, and client satisfaction, we offer a full suite of solutions from BIM clash detection to comprehensive thermographic inspections. Our expert team ensures your project is complying, efficient, and prepared for future demands.
Trust Stonehaven for all your MEP survey and troubleshooting needs. Contact us today for a consultation and discover how we can contribute to the success of your next construction project.