In today’s competitive construction landscape, optimising project costs while maintaining quality and functionality has never been more critical. Value engineering in construction stands out as a vital methodology for achieving this balance, empowering stakeholders to maximise returns on their investments while adhering to timelines and regulations. From concept to completion, value engineering solutions provide a structured approach to enhance project outcomes without compromising on quality.
What Is Value Engineering in Construction?
Value engineering (VE) is a systematic process aimed at enhancing the value of a project by balancing cost efficiency and performance. Originating in manufacturing during the 1940s, VE has become a cornerstone of modern construction management. At its core, value engineering involves a thorough review of project designs, materials, systems, and processes to identify opportunities for cost savings and improved functionality.
When applied effectively, value engineering services can reduce unnecessary expenses, address inefficiencies, and provide innovative alternatives to meet project goals. For instance, a value engineering consultant might propose the use of alternative materials that meet the same durability and safety standards while lowering overall costs.
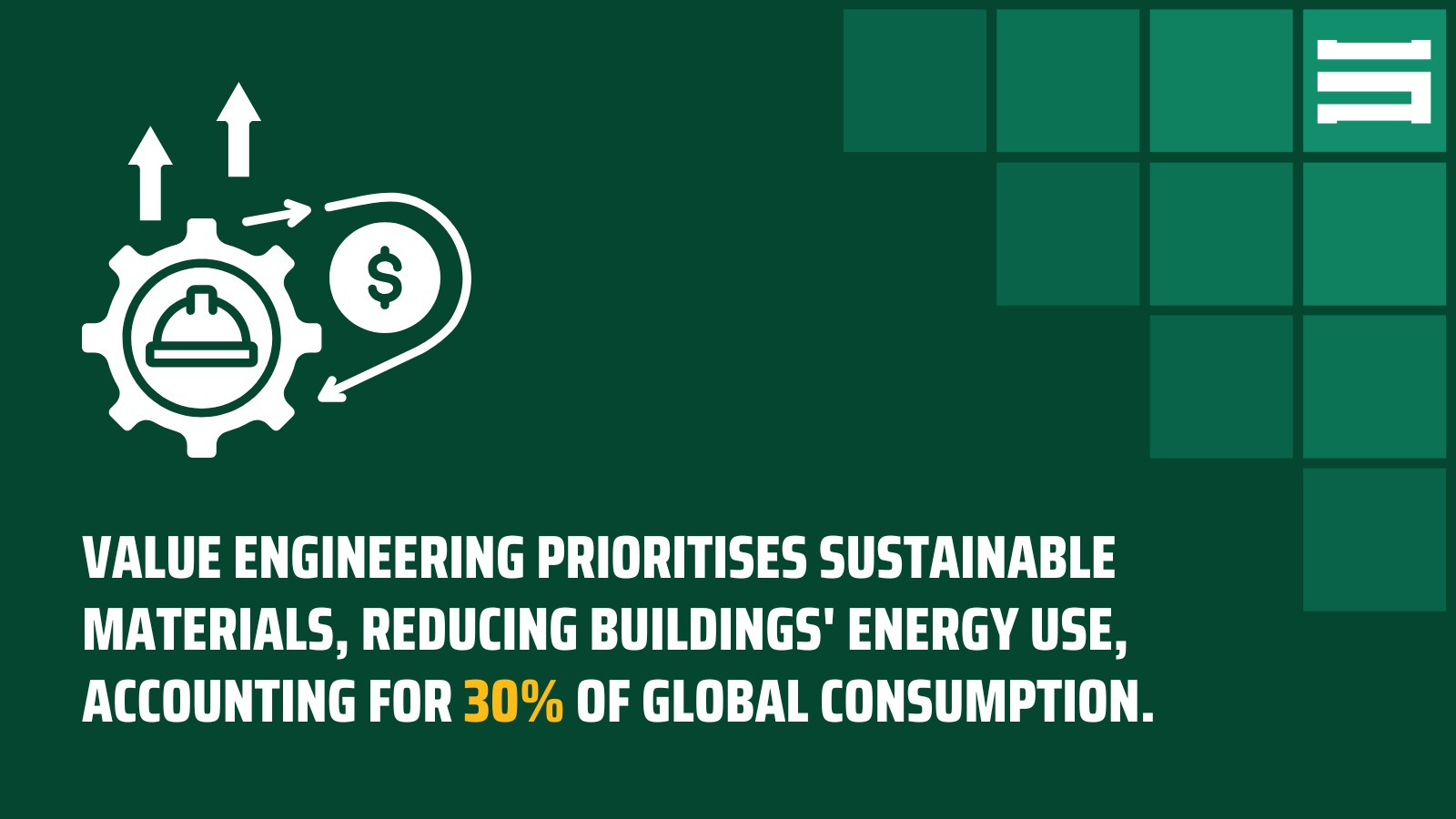
Why Is Value Engineering Important in Construction?
The construction industry often faces challenges such as budget overruns, delays, and complex regulatory requirements. This is where value engineering solutions shine, ensuring projects are delivered on time and within budget, without sacrificing quality.
By integrating value engineering, construction projects have made strides in reducing energy consumption. Sustainable building practices and materials have been prioritised, reducing the environmental footprint of buildings, which account for 30% of global energy consumption.
Key areas where value engineering is transformative include:
- Cost Optimisation: By evaluating material choices and construction methods, value engineering can significantly lower project costs.
- Functionality Improvement: VE ensures projects meet their intended use with optimal performance.
- Sustainability: Many value engineering approaches integrate environmentally friendly materials and energy-efficient systems, aligning with modern green building practices.
Steps of the Value Engineering Process
The six-step value engineering process, as outlined in resources like the Procore Library, provides a structured methodology for systematically enhancing project value. This approach ensures that cost-saving opportunities, functional improvements, and innovative solutions are identified and implemented without compromising quality or performance. Each step focuses on a specific objective and aligns with the overarching goal of maximising efficiency in construction projects.
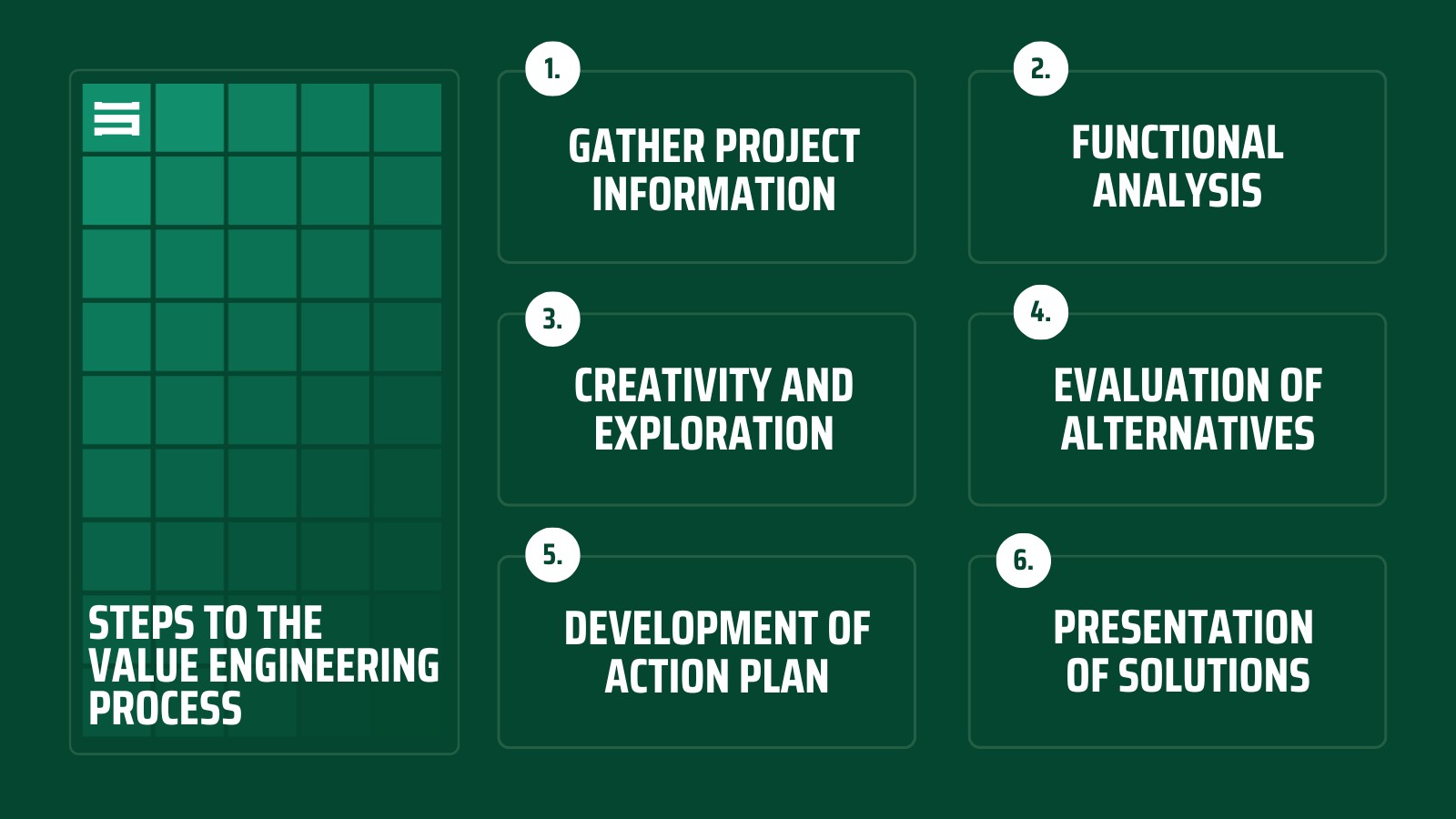
1. Gather Project Information
- Objective: Collect comprehensive project data, including costs, design specifications, timelines, and stakeholder expectations.
- Key Question: What is the overarching goal?
In this foundational step, all relevant details about the project are compiled to establish a clear understanding of its scope and limitations. This includes analysing materials, construction techniques, and financial constraints. Teams may also use tools such as property condition assessment reports to evaluate existing site conditions, helping to identify areas for potential improvement.
2. Functional Analysis
- Objective: Assess the role and necessity of each project component, focusing on its intended function.
- Key Question: What does this element need to accomplish?
This phase involves evaluating each element’s purpose and its contribution to the overall project. Engineers determine whether a specific feature or material is essential, redundant, or could be replaced with a more efficient alternative. For example, is a particular structural system overengineered for the required load? Identifying such inefficiencies ensures that resources are allocated optimally.
3. Creativity and Exploration
- Objective: Explore alternative methods to achieve the same functional outcomes with improved cost-efficiency or performance.
- Key Question: What other methods or materials could achieve this result?
Here, brainstorming and innovative thinking come into play. The team generates creative solutions to challenges identified in earlier steps. For example, substituting conventional building materials with lightweight, eco-friendly alternatives could significantly lower costs while improving sustainability, a key consideration for projects adhering to modern construction codes, such as those in the UAE.
4. Evaluation of Alternatives
- Objective: Analyse proposed alternatives for their feasibility, impact, and alignment with project goals.
- Key Question: Does this option increase the project’s overall value?
In this step, proposed alternatives are rigorously assessed for practicality. Factors such as cost, quality, regulatory compliance, and compatibility with the project’s timeline are considered. For example, prefabrication might reduce construction time and costs but would need evaluation for logistical feasibility and adherence to local regulations as determined by building code consultants.
5. Development of Action Plan
- Objective: Refine promising alternatives, examining their detailed implications on cost, functionality, schedule, and stakeholder expectations.
- Key Question: How do these changes affect the project’s overall performance?
Promising ideas are further developed into actionable plans. This phase often includes detailed calculations, simulations, and stakeholder consultations to determine the real-world impact of proposed changes. For example, an alternative roofing material might save costs in the short term, but lifecycle analyses could reveal greater long-term benefits, such as energy efficiency and reduced maintenance.
6. Presentation of Solutions and Reporting
- Objective: Present the most viable solutions to stakeholders, providing a transparent analysis of their advantages and trade-offs.
- Key Question: What options offer the most balanced improvements?
The final step ensures that stakeholders, including project owners and developers, are well-informed about the proposed changes. Clear, data-backed presentations outline the pros and cons of each option, empowering decision-makers to choose the most suitable alternative. For instance, a sustainable energy system may have a higher initial cost but offer long-term savings and align with the project’s sustainability goals.
Applying the Process in Construction Projects
The six-step value engineering process is a reliable framework for making informed, strategic decisions in construction projects. In dynamic markets like the UAE, this approach ensures compliance with regulations, optimises costs, and enhances project functionality. By following this structured method, project teams and value engineering consultants deliver solutions that not only meet but exceed stakeholder expectations.
Benefits of Value Engineering in Construction
Value engineering (VE) has become a cornerstone of modern construction practices, offering a systematic approach to enhancing project outcomes. By focusing on cost efficiency, functionality, sustainability, and risk management, VE provides tangible benefits that contribute to a project's overall success.
1. Improved Cost Efficiency
Let’s face it: staying on budget is a top priority for any construction project. VE is your secret weapon for eliminating unnecessary expenses without cutting corners. It’s about making smarter choices. For instance, instead of using a high-cost material, VE might suggest an equally durable alternative that’s more affordable. That one change alone can save significant money—and with the right cost consultants you can allocate that budget elsewhere to enhance the project. Think of it as spending strategically, not less.
2. Enhanced Project Quality
Here’s a common misconception: cutting costs means sacrificing quality. Not with VE. It’s a process that ensures your project delivers optimal functionality, often exceeding expectations. By analysing every design element, VE ensures the finished product isn’t just fit for purpose—it’s better. Imagine upgrading to a more efficient HVAC system through VE. While the upfront cost might seem higher, the long-term benefits—better performance, reduced energy bills—are undeniable. Quality isn’t just preserved; it’s amplified.
3. Sustainability and Compliance
Sustainability is no longer optional—it’s essential. VE helps integrate green building technologies, energy-efficient systems, and sustainable materials into your project. Beyond environmental benefits, this approach enhances compliance with building codes and regulations. Partnering with building code consultants during the VE process ensures you meet local standards while adopting eco-friendly practices. This not only reduces your project’s carbon footprint but also holds it accountable to sustainable thinking and makes it more appealing to modern, environmentally conscious investors and buyers. (Read more on carbon accounting strategies here)
4. Reduced Risk
Every project faces risks, but VE ensures you tackle them head-on. By including a detailed risk assessment, VE identifies potential pitfalls—whether it’s a design flaw, material failure, or construction inefficiency—and offers solutions to avoid them. Reducing these risks minimises delays, avoids costly overruns, and ensures a stronger, longer-lasting structure. In short, VE builds confidence alongside buildings.
5. Faster Project Delivery
Time is money, and VE is your time-saver. By simplifying designs and optimising construction processes, VE cuts down project timelines without compromising quality. Techniques like modular construction, often suggested in VE analysis, accelerate timelines while maintaining standards. This means you can bring your project to market faster, delivering value to end-users sooner.
Why Value Engineering Matters
At its core, value engineering is about more than cost savings—it’s about creating smarter, more sustainable projects that deliver exceptional results. It’s a win-win: better outcomes for stakeholders and more efficient use of resources. If you’re not leveraging VE in your construction projects, you’re leaving significant value on the table. Ready to transform your approach? It’s time to make value engineering part of your playbook.
Opportunities in Value Engineering
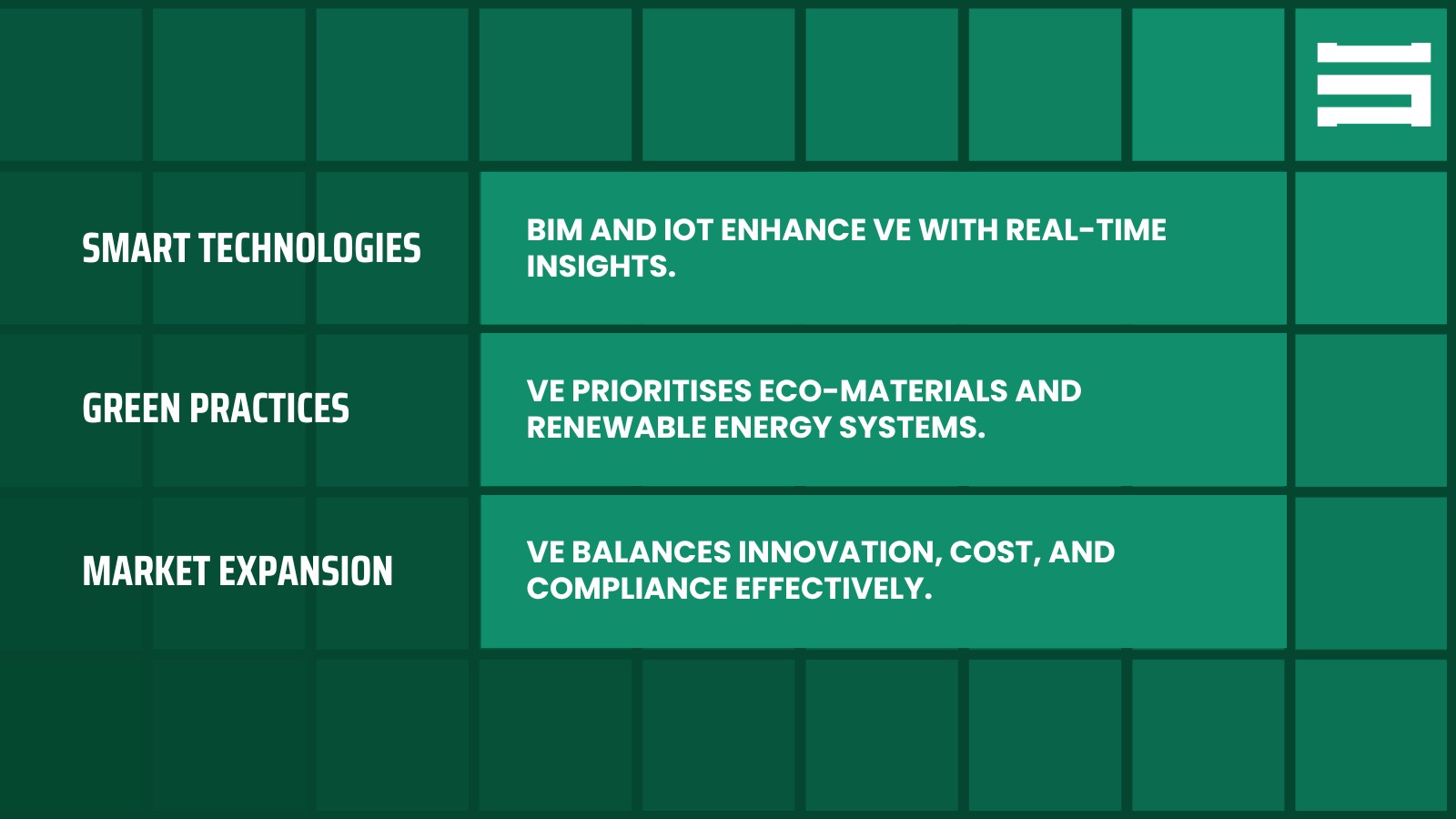
The evolution of construction technologies and sustainable building practices presents new opportunities for value engineering, particularly in fast-growing regions like the UAE.
1. Integration of Smart Technologies
Emerging tools such as BIM (Building Information Modelling) and IoT (Internet of Things) are revolutionising VE processes by providing precise data analysis and real-time insights.
2. Green Construction Practices
As sustainability becomes a priority, value engineering supports the adoption of eco-friendly materials and renewable energy systems.
3. Expansion in UAE Markets
The UAE construction sector, known for its ambitious projects, relies heavily on value engineering to balance innovation with cost control. From luxury developments to infrastructure projects, VE ensures compliance with international standards and local regulations.
Challenges in Implementing Value Engineering
Despite its benefits, value engineering is not without challenges:
- Resistance to Change: Stakeholders may be hesitant to adopt alternative materials or methods due to familiarity with traditional approaches.
- Balancing Cost and Quality: Ensuring cost reductions don’t compromise safety, durability, or aesthetics can be complex.
- Regulatory Compliance: VE must align with stringent building codes, particularly in regions like the UAE, where building code consultants play a pivotal role.
- Stakeholder Communication: Collaborative engagement between architects, contractors, and consultants is critical to achieving consensus on proposed changes.
Emerging Trends in Value Engineering
- Digital Transformation: The adoption of AI and advanced analytics is streamlining the VE process, enabling more accurate cost and risk assessments.
- Focus on Lifecycle Costs: Value engineering now extends beyond initial construction, considering operational and maintenance costs for long-term benefits. (Read more about life cycle costing here)
- Collaboration with Specialised Consultants: Companies are increasingly seeking experts in property condition assessment companies to provide insights into site-specific VE opportunities.
Conclusion
Value engineering has proven to be a game-changer time after time for the construction industry, offering a systematic approach to cost optimisation, quality enhancement, and sustainability. By addressing challenges head-on and embracing new opportunities, value engineering solutions continue to redefine the possibilities of modern construction.
Whether you’re a developer, contractor, or architect, adopting value engineering principles can lead to more efficient and successful projects. As construction trends evolve, the role of value engineering services in driving innovation and cost-effectiveness remains pivotal.
About us
Stonehaven is a trusted project management company and construction consultant based in Dubai, offering comprehensive construction management services across the UAE with offices located in Dubai, UK and Sri Lanka. As one of the leading project management companies in Dubai, we manage projects from inception to completion, ensuring quality, efficiency, and cost-effectiveness at every stage.
We deliver value through expert project management consultancy services, tailored to meet the unique needs of each client. Our core services include Cost Management, Project Management, Construction Supervision, Engineering Support, Design Support, and Marketing & Communications. Whether you’re looking for construction consultants or project managers in the UAE and wider GCC region, Stonehaven is your trusted partner for achieving excellence in your next project.
We specialise in providing industry-leading value engineering solutions to transform your construction projects. Our team of experienced value engineering consultants and building code consultants bring a wealth of expertise to every phase of your project, ensuring compliance, quality, and cost efficiency. Whether it’s a building risk assessment UAE or a detailed property condition assessment report, we are committed to delivering value at every step.
Discover how our tailored value engineering services can elevate your next project. Visit Stonehaven today and take the first step towards smarter, more sustainable construction.